How Rotomolding Meets the Needs of Agricultural Equipment Manufacturers
Rotomolding , or rotational molding , is really a flexible process used to produce different useless plastic products. Despite its advantages, it gift suggestions a few challenges that manufacturers must handle to make sure quality outcomes. This informative article explores some traditional dilemmas in Rotomolding and offers useful methods to undertake them effectively.

Irregular Wall Width
One of the very repeated challenges in rotomolding is reaching even wall thickness. Irregular walls may result in poor locations and defects in the ultimate product. To over come this, manufacturers must ensure maximum shape turning pace and also heat circulation throughout the process. Additionally, using supreme quality products and calibrating gear correctly can help obtain standard wall thickness.
Area Flaws
Surface problems such as for instance pinholes, pockets, and rough textures are normal in rotomolded products. These imperfections often result from insufficient ventilation or incorrect cooling. To minimize area problems, make certain that molds are properly vented release a stuck air and gases. Employing a managed cooling process may also subscribe to smoother finishes and higher-quality products.
Product Collection and Consistency
Choosing the right product for rotomolding is crucial for making sturdy and trusted products. Nevertheless, inconsistencies in resin quality, additives, or colorants can lead to subpar results. To handle this problem, manufacturers must source products from reputable providers with a background of giving regular quality. Typical testing and quality control methods may more assure product reliability and maximum performance.
Minimizing Warping and Distortion
Warping and distortion arise when parts great unevenly or also quickly. These issues can bargain the architectural strength of the product. To combat this, companies should use standard cooling methods and ensure that the shapes are adequately made to support also temperature distribution. Changing pattern times and employing post-mold chilling techniques also can lessen warping and distortion.
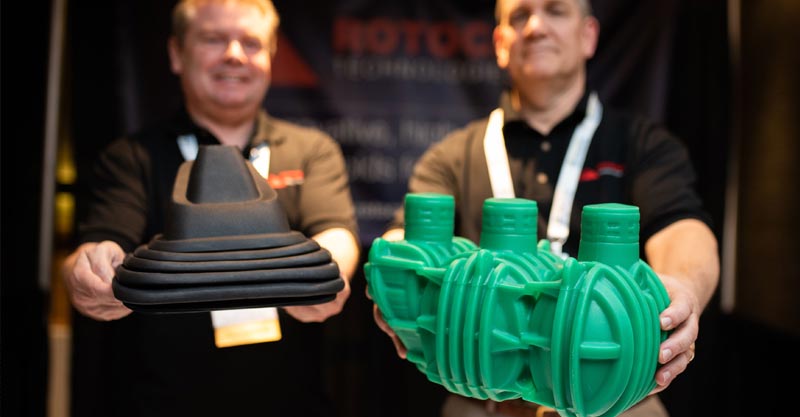
Final Feelings
While rotomolding presents unique difficulties, understanding and addressing these issues may cause increased solution quality and customer satisfaction. Through the use of alternatives such as optimizing wall depth, reducing area problems, ensuring material reliability, and minimizing warping, manufacturers can improve their rotomolding processes. Overcoming these issues not only benefits creation effectiveness but in addition assures the endurance and efficiency of the final products.